Home » Wind Turbine » Direct Drive Wind Turbine vs. Geared Drive Wind Turbine
Direct Drive Wind Turbine vs. Geared Drive Wind Turbine
According to the drivetrain condition in a wind generator system, wind turbines can be classified as either direct drive or geared drive groups. To increase the generator rotor rotating speed to gain a higher power output, a regular geared drive wind turbine typically uses a multi-stage gearbox to take the rotational speed from the low-speed shaft of the blade rotor and transform it into a fast rotation on the high-speed shaft of the generator rotor. The advantages of geared generator systems include lower cost and smaller size and weight. However, utilization of a gearbox can significantly lower wind turbine reliability and increase turbine noise level and mechanical losses.
Comparison of Direct Drive and Geared Generator Systems
Different direct-drive and geared generator systems of the wind turbines have been discussed by a number of authors. According to the comparison of different direct drive and geared generator systems discussed, the features of the systems can be summarized as the following:
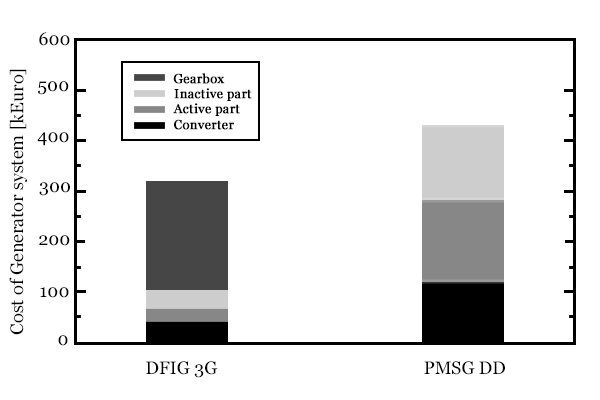
Figure 1
Figure 1 depicts the cost of both 3 MW doubly-fed induction generator system with three stage gearbox and direct drive permanent magnet synchronous generator system including the gearbox, the inactive part, the active part and the converter. If it is possible to reduce the cost of direct-drive permanent magnet synchronous generator system by the cost of doubly-fed induction generator system with three stage gearbox or lower than it, then the direct-drive permanent magnet synchronous generator system can be the most suitable generator concept, because the energy yield of this system is the maximum. Therefore, to reduce the cost of direct drive generator systems will be the most important issue in both the electromagnetic design and the mechanical design.
The necessity of new wind power system comes from recent studies which have shown that gearboxes are responsible for the greatest percentage of outage time. Wind turbine manufacturers are turning away from the industry-standard gearboxes and generators in a bid to boost the reliability and reduce the cost of wind power.
In conventional wind turbines, the gearbox increases the speed of the wind-driven rotor several hundred-fold, which radically reduces the size of the generator required. In the direct-drive generator for wind turbine, the rotor is directly connected to the rotor hub. Direct-drive generators operate at the same speed as the turbine's blades and must therefore be much bigger.
Even for a large direct-drive generator, with a diameter of several meters, the air-gap should not exceed a few millimeters, to avoid excessive magnetization requirements. This means that the mechanical construction has to be very rigid, in order to maintain the air-gap against the powerful force of attraction between the rotor and the stator. This stiffness requirement applies to the load path through the rotor, the shaft, the bearings and the stator. Thus the stiffness places a practical and economical limit on the diameter of a conventionally built generator.
Because of that the direct drive concept is operated in low speed. When scaling up the wind turbine, the rotational speed is decreased more and more considering the tip speed limitation. In order to scale up the power of the direct-drive generator, the torque, T must be thus increased in inverse proportion to the decrease of the mechanical angular speed, wm by:
The generator power, P can be also defined as a function of the tangential force density, Fd , the air gap diameter, Dg , the axial length, ls and the mechanical angular speed as shown in:
Direct-drive generator has a larger diameter to produce higher torque because the torque is proportional to the air gap diameter squared. Thus higher torque demands large air gap diameter of the generator and high tangential force. This results in the increase of materials to maintain the air gap in proper deflection against the normal stress between the rotor and stator. Therefore, the concept of direct-drive generator is operated in low speed and has the disadvantages such as high large diameter, heavy mass, torque rating and high cost compared to the concept of geared generator. That is why the concept of direct-drive generator is designed with a large diameter and small pole pitch to increase the efficiency, to reduce the active material and to keep the end winding losses small.
Direct-drive permanent magnet machines have several advantages compared to the electrically excited machines. They can be listed as:
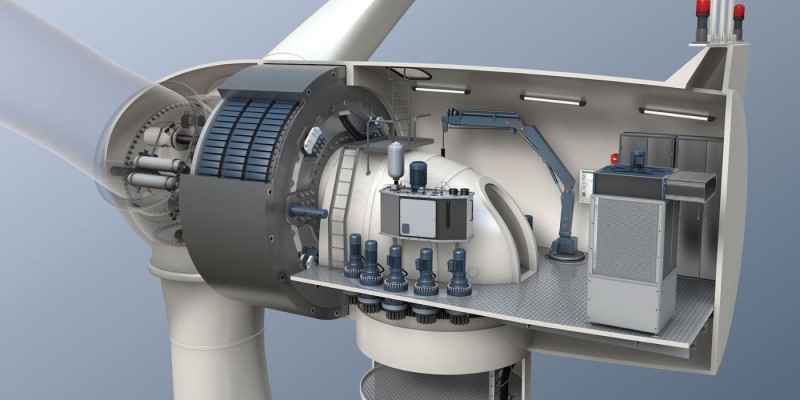
Because of those advantages permanent magnet machines are considered as the promising electromagnetic structure for direct-drive generator. By eliminating the multi-stage gearbox from a generator system, the generator shaft is directly connected to the blade rotor. Therefore, the direct-drive concept is more superior in terms of energy efficiency, reliability, and design simplicity. Due to its advantages of low noise and high efficiency, direct-drive wind turbines will be the preferred choice of the wind power industry in the future.
Comparison of Direct Drive and Geared Generator Systems
Different direct-drive and geared generator systems of the wind turbines have been discussed by a number of authors. According to the comparison of different direct drive and geared generator systems discussed, the features of the systems can be summarized as the following:
- Considering the energy yield and reliability, the direct drive generator systems seem to be more powerful compared to geared drive systems, especially for offshore.
- The permanent magnet synchronous generator with one stage gearbox has the highest ratio of the annual energy yield to cost.
- The direct-drive permanent magnet synchronous generator system (PMSG DD) is more superior compared to other systems in terms of losses and energy yield.
- The doubly-fed induction generator system with three stage gearbox (DFIG 3G) seems lightweight and low-cost solution.
- Different generator systems can be arranged in the order of high cost as (direct-drive electrically excited synchronous generator) > (direct-drive permanent magnet synchronous generator) > (permanent magnet synchronous generator with one stage gearbox) > (doubly-fed induction generator system with three stage gearbox).
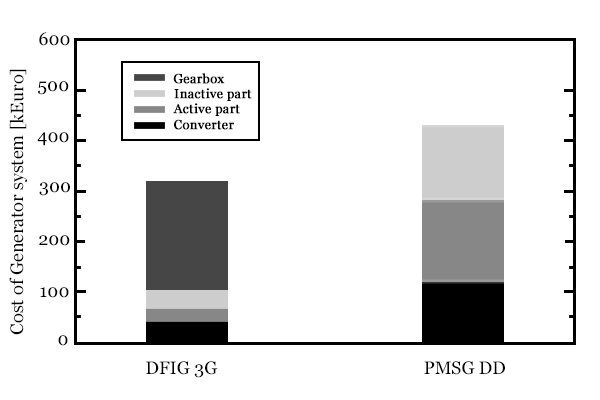
Figure 1
The necessity of new wind power system comes from recent studies which have shown that gearboxes are responsible for the greatest percentage of outage time. Wind turbine manufacturers are turning away from the industry-standard gearboxes and generators in a bid to boost the reliability and reduce the cost of wind power.
In conventional wind turbines, the gearbox increases the speed of the wind-driven rotor several hundred-fold, which radically reduces the size of the generator required. In the direct-drive generator for wind turbine, the rotor is directly connected to the rotor hub. Direct-drive generators operate at the same speed as the turbine's blades and must therefore be much bigger.
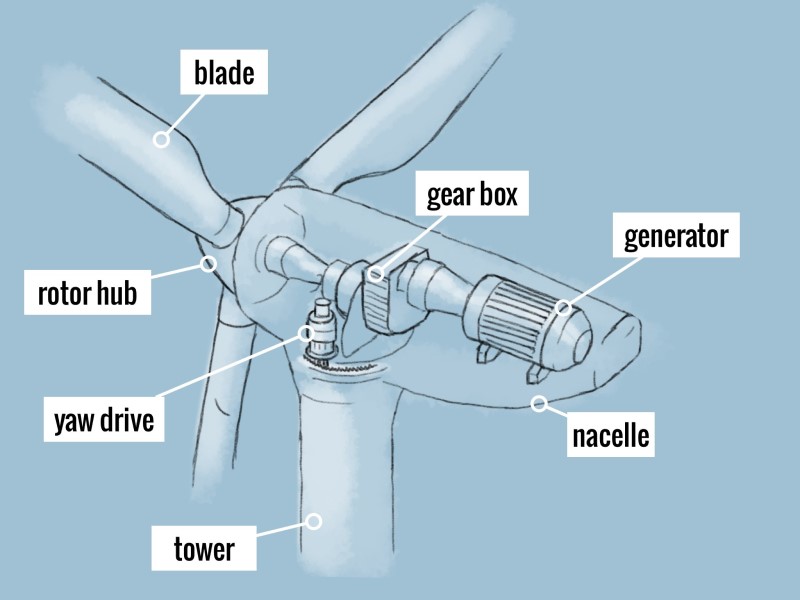
Even for a large direct-drive generator, with a diameter of several meters, the air-gap should not exceed a few millimeters, to avoid excessive magnetization requirements. This means that the mechanical construction has to be very rigid, in order to maintain the air-gap against the powerful force of attraction between the rotor and the stator. This stiffness requirement applies to the load path through the rotor, the shaft, the bearings and the stator. Thus the stiffness places a practical and economical limit on the diameter of a conventionally built generator.
Because of that the direct drive concept is operated in low speed. When scaling up the wind turbine, the rotational speed is decreased more and more considering the tip speed limitation. In order to scale up the power of the direct-drive generator, the torque, T must be thus increased in inverse proportion to the decrease of the mechanical angular speed, wm by:
(1)![]()
The generator power, P can be also defined as a function of the tangential force density, Fd , the air gap diameter, Dg , the axial length, ls and the mechanical angular speed as shown in:
(2)![]()
Direct-drive generator has a larger diameter to produce higher torque because the torque is proportional to the air gap diameter squared. Thus higher torque demands large air gap diameter of the generator and high tangential force. This results in the increase of materials to maintain the air gap in proper deflection against the normal stress between the rotor and stator. Therefore, the concept of direct-drive generator is operated in low speed and has the disadvantages such as high large diameter, heavy mass, torque rating and high cost compared to the concept of geared generator. That is why the concept of direct-drive generator is designed with a large diameter and small pole pitch to increase the efficiency, to reduce the active material and to keep the end winding losses small.
Direct-drive permanent magnet machines have several advantages compared to the electrically excited machines. They can be listed as:
- Higher power to weight ratio;
- Improvement in the efficiency;
- High energy yield and light weight;
- No additional power supply for the field excitation, Higher reliability without slip rings.
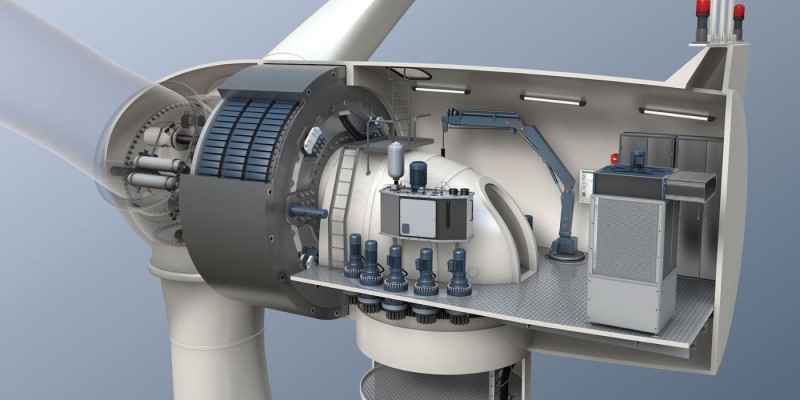
Because of those advantages permanent magnet machines are considered as the promising electromagnetic structure for direct-drive generator. By eliminating the multi-stage gearbox from a generator system, the generator shaft is directly connected to the blade rotor. Therefore, the direct-drive concept is more superior in terms of energy efficiency, reliability, and design simplicity. Due to its advantages of low noise and high efficiency, direct-drive wind turbines will be the preferred choice of the wind power industry in the future.
Post a Comment:
You may also like:
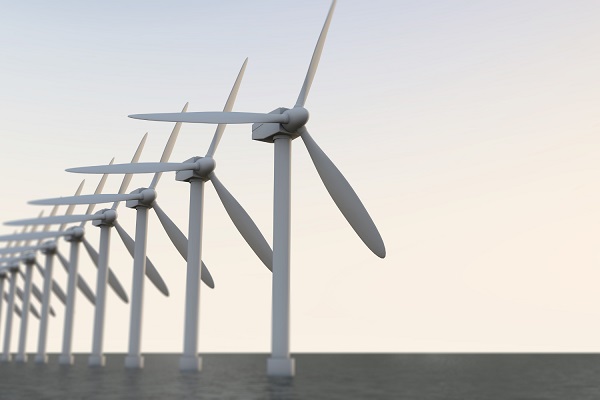
Featured Articles
Horizontal Axis vs. Vertical Axis
Wind turbines are machines that generate electricity from the kinetic energy of the wind. In history, they were more ...
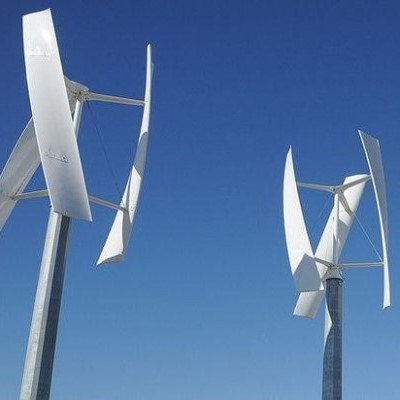
Horizontal Axis Wind Turbine Design
Today, the most common design of wind turbine is the horizontal axis wind turbine (HAWT). That is, the axis of rotation is ...
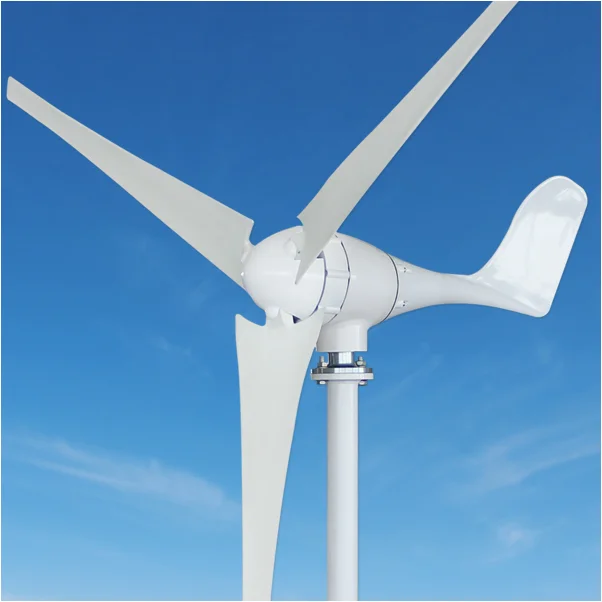
Overvoltage Protection for Wind ...
Due to their principle of operation, wind turbines have to be set up outdoors and are used in a wide range of ...
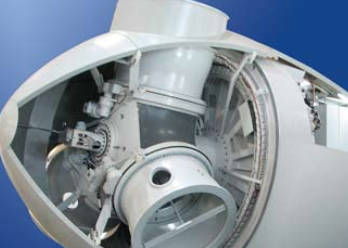
What is a Wind Turbine?
Wind turbines are devices that convert the kinetic energy from the wind into mechanical power, which can then be used to generate ...
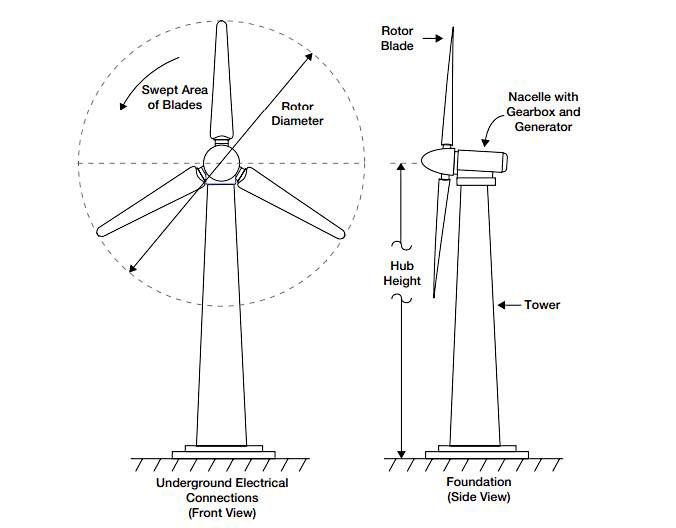
Household Wind Energy System Components
Basic parts of home wind energy systems generally comprise a rotor, a generator or alternator mounted on a frame, a tail ...
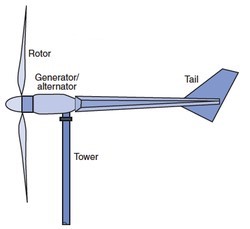