Home » Wind Turbine » Horizontal Axis Wind Turbine Design
Horizontal Axis Wind Turbine Design
Today, the most common design of wind turbine is the horizontal axis wind turbine (HAWT). That is, the axis of rotation is parallel to the ground. HAWT rotors are usually classified according to the rotor orientation (upwind or downwind of the tower), hub design (rigid or teetering), rotor control (pitch vs. stall), number of blades (usually two or three blades), and how they are aligned with the wind (free yaw or active yaw).
The principal subsystems of a typical (land-based) horizontal axis wind turbine are shown in picture below. These include:
The main options in wind turbine design and construction include:
A short introduction to and overview of some of the most important components follows.
Generator
Nearly all wind turbines use either induction or synchronous generators. These designs entail a constant or nearly constant rotational speed when the generator is directly connected to a utility network. If the generator is used with power electronic converters, the turbine will be able to operate at variable speed.
Many wind turbines installed in grid connected applications use squirrel cage induction generators (SQIG). A SQIG operates within a narrow range of speeds slightly higher than its synchronous speed (a four-pole generator operating in a 60 Hz grid has a synchronous speed of 1800 rpm). The main advantages of this type of induction generator are that it is rugged, inexpensive, and easy to connect to an electrical network. An increasingly popular option today is the doubly fed induction generator (DFIG). The DFIG is often used in variable-speed applications.
An increasingly popular option for utility-scale electrical power generation is the variable speed wind turbine. There are a number of benefits that such a configuration offers, including the reduction of wear and tear on the wind turbine and potential operation of the wind turbine at maximum efficiency over a wide range of wind speeds, yielding increased energy capture. Although there are a large number of potential hardware options for variable-speed operation of wind turbines, power electronic components are used in most variable-speed machines currently being designed. When used with suitable power electronic converters, either synchronous or induction generators of either type can run at variable speed.
Rotor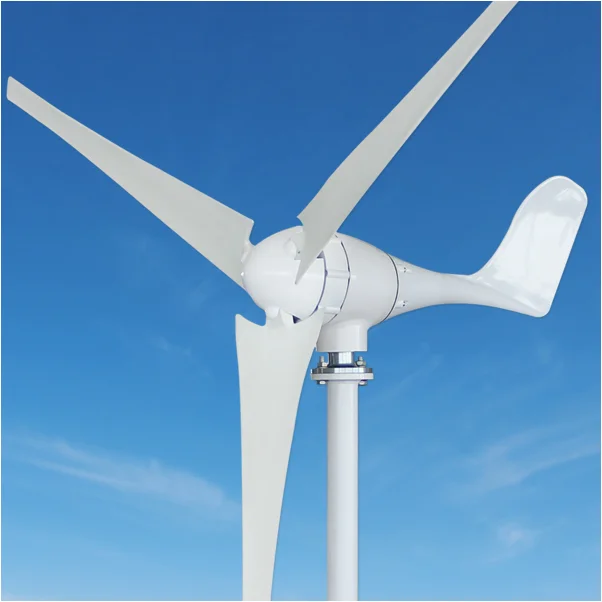
The rotor consists of the hub and blades of the wind turbine. These are often considered to be the turbine’s most important components from both a performance and overall cost standpoint.
Most turbines today have upwind rotors with three blades. There are some downwind rotors and a few designs with two blades. Single-blade turbines have been built in the past, but are no longer in production. Some intermediate-sized turbines used fixed-blade pitch and stall control. Most manufacturers use pitch control, and the general trend is the increased use of pitch control, especially in larger machines. The blades on the majority of turbines are made from composites, primarily fiberglass or carbon fiber reinforced plastics (GRP or CFRP), but sometimes wood/epoxy laminates are used.
Tower and Foundation
This category includes the tower itself and the supporting foundation. The principal types of tower design currently in use are the free-standing type using steel tubes, lattice (or truss) towers, and concrete towers. For smaller turbines, guyed towers are also used.
Tower height is typically 1 to 1.5 times the rotor diameter, but in any case, is normally at least 20 m. Tower selection is greatly influenced by the characteristics of the site. The stiffness of the tower is a major factor in wind turbine system dynamics because of the possibility of coupled vibrations between the rotor and tower. For turbines with downwind rotors, the effect of tower shadow (the wake created by air flow around a tower) on turbine dynamics, power fluctuations, and noise generation must be considered. For example, because of the tower shadow, downwind turbines are typically noisier than their upwind counterparts.
The principal subsystems of a typical (land-based) horizontal axis wind turbine are shown in picture below. These include:
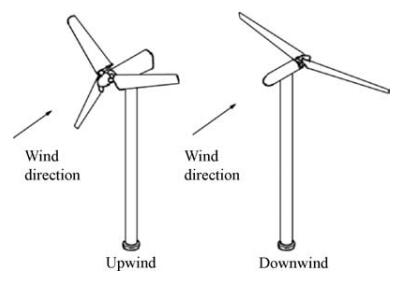
- The rotor, consisting of the blades and the supporting hub.
- The drive train, which includes the rotating parts of the wind turbine (exclusive of the rotor); it usually consists of shafts, gearbox, coupling, a mechanical brake, and the generator.
- The nacelle and main frame, including wind turbine housing, bedplate, and the yaw system.
- The tower and the foundation.
- The machine controls.
- The balance of the electrical system, including cables, switchgear, transformers, and possibly electronic power converters.
-
number of blades (commonly two or three);
- rotor orientation: downwind or upwind of tower;
- blade material, construction method, and profile;
- hub design: rigid, teetering, or hinged;
- power control via aerodynamic control (stall control) or variable-pitch blades (pitch control);
- fixed or variable rotor speed;
- orientation by self-aligning action (free yaw), or direct control (active yaw);
- synchronous or induction generator (squirrel cage or doubly fed);
- gearbox or direct drive generator.
Generator
Nearly all wind turbines use either induction or synchronous generators. These designs entail a constant or nearly constant rotational speed when the generator is directly connected to a utility network. If the generator is used with power electronic converters, the turbine will be able to operate at variable speed.
Many wind turbines installed in grid connected applications use squirrel cage induction generators (SQIG). A SQIG operates within a narrow range of speeds slightly higher than its synchronous speed (a four-pole generator operating in a 60 Hz grid has a synchronous speed of 1800 rpm). The main advantages of this type of induction generator are that it is rugged, inexpensive, and easy to connect to an electrical network. An increasingly popular option today is the doubly fed induction generator (DFIG). The DFIG is often used in variable-speed applications.
An increasingly popular option for utility-scale electrical power generation is the variable speed wind turbine. There are a number of benefits that such a configuration offers, including the reduction of wear and tear on the wind turbine and potential operation of the wind turbine at maximum efficiency over a wide range of wind speeds, yielding increased energy capture. Although there are a large number of potential hardware options for variable-speed operation of wind turbines, power electronic components are used in most variable-speed machines currently being designed. When used with suitable power electronic converters, either synchronous or induction generators of either type can run at variable speed.
Rotor
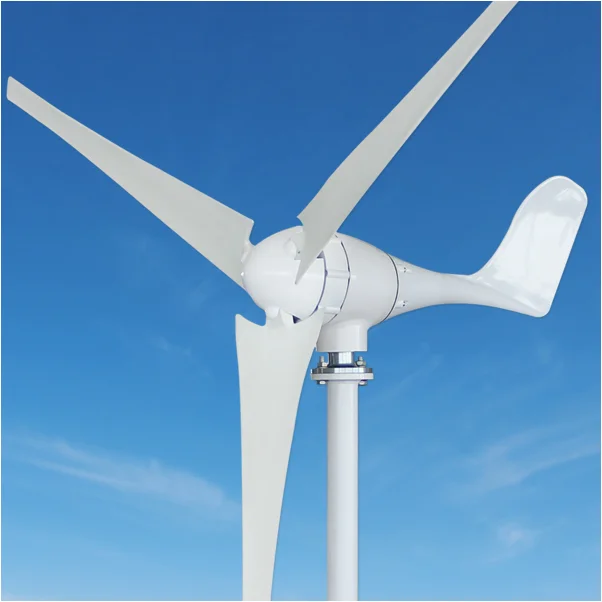
The rotor consists of the hub and blades of the wind turbine. These are often considered to be the turbine’s most important components from both a performance and overall cost standpoint.
Most turbines today have upwind rotors with three blades. There are some downwind rotors and a few designs with two blades. Single-blade turbines have been built in the past, but are no longer in production. Some intermediate-sized turbines used fixed-blade pitch and stall control. Most manufacturers use pitch control, and the general trend is the increased use of pitch control, especially in larger machines. The blades on the majority of turbines are made from composites, primarily fiberglass or carbon fiber reinforced plastics (GRP or CFRP), but sometimes wood/epoxy laminates are used.
Tower and Foundation
This category includes the tower itself and the supporting foundation. The principal types of tower design currently in use are the free-standing type using steel tubes, lattice (or truss) towers, and concrete towers. For smaller turbines, guyed towers are also used.
Tower height is typically 1 to 1.5 times the rotor diameter, but in any case, is normally at least 20 m. Tower selection is greatly influenced by the characteristics of the site. The stiffness of the tower is a major factor in wind turbine system dynamics because of the possibility of coupled vibrations between the rotor and tower. For turbines with downwind rotors, the effect of tower shadow (the wake created by air flow around a tower) on turbine dynamics, power fluctuations, and noise generation must be considered. For example, because of the tower shadow, downwind turbines are typically noisier than their upwind counterparts.
Post a Comment:
You may also like:
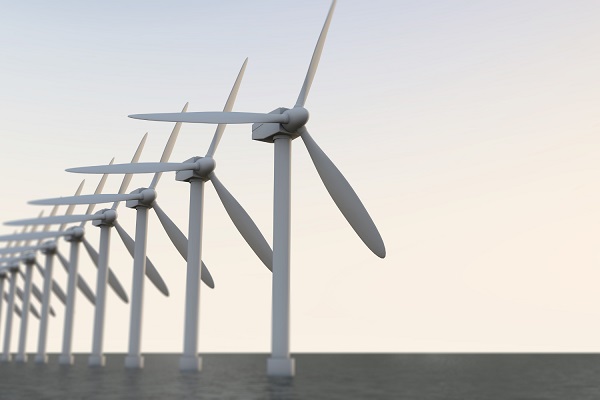
Featured Articles
Horizontal Axis vs. Vertical Axis
Wind turbines are machines that generate electricity from the kinetic energy of the wind. In history, they were more ...
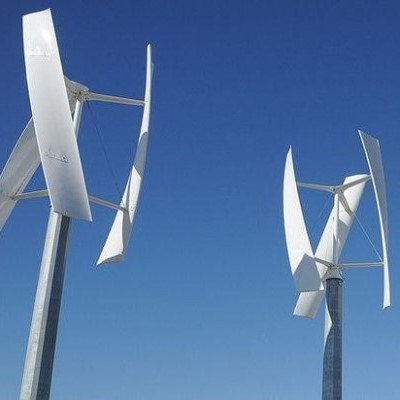
Wind Turbine Glossary
Wind energy is the kinetic energy that is present in moving air. The amount of potential energy depends mainly on wind speed, but ...
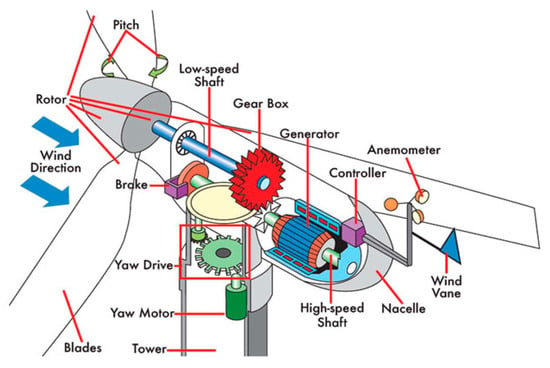
Household Wind Energy System Components
Basic parts of home wind energy systems generally comprise a rotor, a generator or alternator mounted on a frame, a tail ...
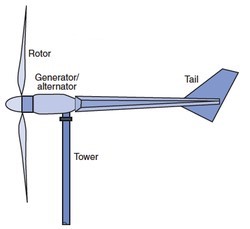
What is a Wind Turbine?
Wind turbines are devices that convert the kinetic energy from the wind into mechanical power, which can then be used to generate ...
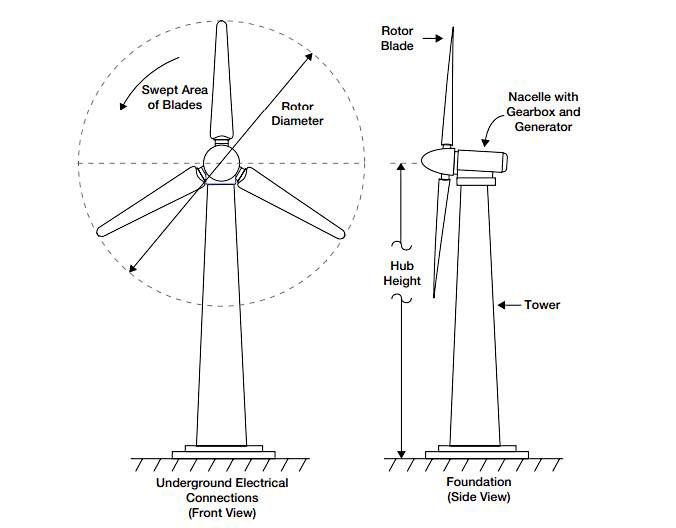
Overvoltage Protection for Wind ...
Due to their principle of operation, wind turbines have to be set up outdoors and are used in a wide range of ...
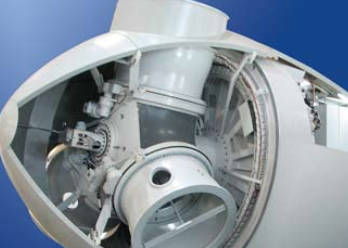