Home » Wind Energy » What is the Wind Energy Conversion System?
What is the Wind Energy Conversion System?
Due to technical and economic visibility, wind power has emerged as one of the most promising renewable energy sources (RES) in recent years. Wind energy capacity can range from a few kilowatts to many megawatts and can be found in many applications. Wind energy can be used in both minor off-grid systems and substantial wind farms connected to the grid. This sort of distributed generation poses issues with the interconnection system due to the absence of active and reactive power control.
Consequently, this approach necessitates careful control, modeling, and choosing a suitable wind power system. The widespread use of wind power has been directly tied to the development of the technology for wind turbines and control technologies over the previous two decades. In this regard, about 102 GW of wind power capacity was added in 2021. Annual increases raised the total capacity by 13.5%, reaching more than 845 GW. In terms of market share, China dominated the market, followed by the USA, UK, Brazil, and Vietnam. Figure 1 indicates growth in installed global wind capacity to approximately 845 by the end of 2021 compared to 651 GW in 2019. It is expected that installed wind capacity will increase dramatically over the next few years due to the continuing desire for alternative energy sources.
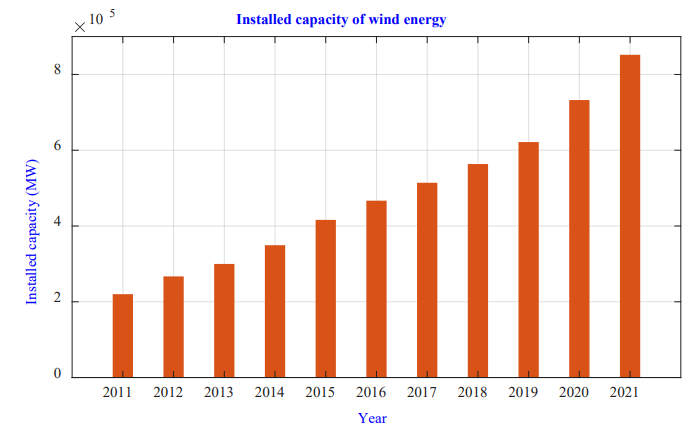
Figure 1
Despite the incredible expansion of wind energy, researchers face numerous hurdles, including the unpredictability of the wind’s nature, grid connection, and the positioning of wind turbines. This blog proposes a widespread review of the impact of converters on wind energy conversion with its operation, control, and related issues.
Wind Energy Conversion System
The wind energy conversion system (WECS) contains wind turbines and converters. Using wind turbines to extract the wind’s mechanical energy, the generators convert it into electrical energy, and the converter system is in charge of transferring the generated energy to the power network or a battery bank. When converting wind energy to electricity at a variable speed, the most commonly utilized generators are synchronous and doubly-fed induction generators (DFIG). When using induction generators, the rotor and stator are both linked directly to the network, but the electronic converter acts as a mediator between the two. Since the rotor circuit may independently change the amplitude and frequency of the produced voltage, the DFIG has long been the preferred choice for large, variable-speed WECS that are connected directly to the electrical network, as illustrated in Figure 2a.
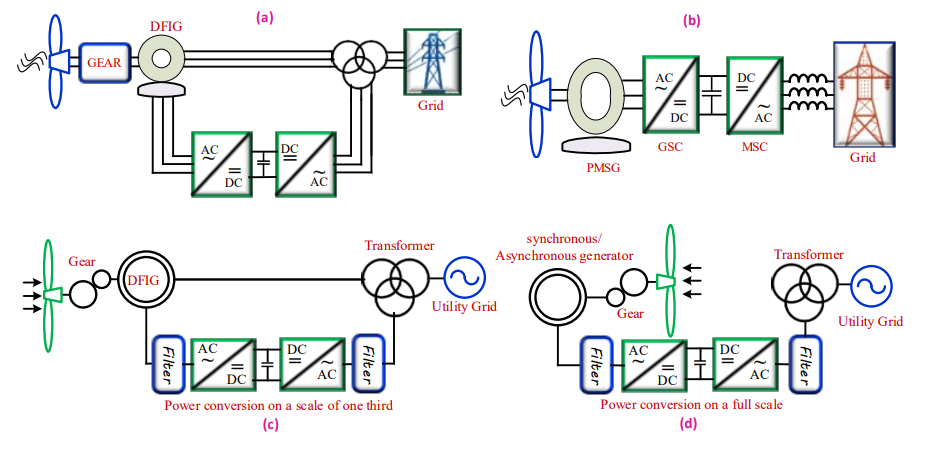
Figure 2 (a-d)
Generators that generate synchronous power are disconnected from the power distribution grid. As a result, they are included in systems that utilize full-scale converters. Due to the lack of a gearbox, the multipole permanent magnet synchronous generator (PMSG) has been the preferred alternative in recent years, reducing WECS losses, reducing maintenance requests, and enhancing system efficiency and dependability.
Figure 2b illustrates its configuration. Dc-links frequently employ a chopper circuit to disperse power in the event of grid disruptions. When compared to DFIG, PMSG offers the following advantages: no external stimulating current is required; high reliability; lightweight; low maintenance; small size; and high efficiency. The fundamental elements of a WTS’s control system, including the turbine, generator, filter, and converter, as displayed in Figure 2a–d. It is possible for the designed wind turbine to either be of the kind seen in Figure 2c or of the kind depicted in Figure 2d.
Previously, the usage of permanent magnet synchronous generators was recognized primarily in tiny WT but not in large-scale power generation due to the huge and heavy permanent magnets required. The usage of wind turbines based on permanent magnet generators (PMG) is quickly increasing because of the advancement of semiconductor switches and the improvement in efficiency and reliability; also, the innovation of materials utilized in the rotor of the generator has permitted the use of PMG at high power. For example, a permanent magnet-based-high-temperature superconductor is used in the rotor to achieve higher magnetic density: a 15-mm thick segment of permanent magnets can generate the same magnetic field as a 100–150-mm section of copper windings. Furthermore, the setting up of a gearbox, which is mandatory for large and medium WT, can be avoided using direct drive variable speed. Due to its simplicity, the direct drive wind turbine with PMG is now employed in the wind power system as the most promising one.
Wind Turbine Operation
The WECS uses improved control algorithms due to the rapid advancement of industry expertise. In a WECS, the wind’s kinetic energy is transformed to mechanical one using the WT, which is subsequently transformed into electrical energy. Because wind power is not ready to be integrated into the grid, several converter topologies have been developed to properly govern the grid-side converter (GSC) and the machine-side converter.
As a response, the fundamental control of WECS is used to serve the electricity network’s needs at different wind speeds, as presented in Figure 3a. The unpredictable nature of the speed of the wind and the variability of the climate highly influences wind energy’s dependability. Because of this, it is essential to understand the nature of wind and identify its operating areas to effectively integrate the WTs into the utility grid according to the speed measured. Thus, for a particular range of the speed of wind constrained by cut-out (Vcut-in) and cut-in (Vcut-out) speeds, WT can be used to harvest the accessible wind power, as explained in Figure 3a,b. The typical variable and fixed wind speed power curves are shown in Figure 3b.
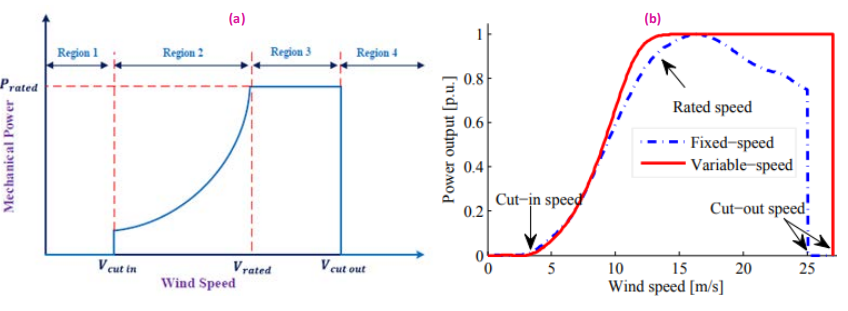
Figure 3 (a-b)
Accordingly, the following is a breakdown of WT’s operational areas:
Wind Turbine Configurations
In a WT, the kinetic or mechanical energy of the wind is converted into electricity. When connecting WTs to electrical grids, three primary configurations may be utilized for this purpose. An induction machine is a typical cage-rotor induction generator that is promptly linked to the utility grid without needing a power exchanger. Reactive power is necessary for the induction machine to work. Both the utility power system and machine terminal capacitors can be used for this purpose. These devices are incapable of delivering any reactive power. DFIGs are used in the second kind of design, which involves the usage of a wound-rotor. Slip rings are used to capture electricity from a rotating rotor at a slip frequency. This ac power must flow via a converter-based rectifier and inverter system to be converted to a voltage and frequency compatible with the electric power system. Because of this configuration, the size winding of the stator generator can be reduced by 25–30%, with the converters compensating for the power discrepancy between the generator and rotor power. On the other hand, the expense of converters increases the overall cost of such a system. Variable voltage and variable frequency outputs are produced using a permanent or conventional magnet synchronous generator in the third kind of WT architecture. Therefore, an inverter and rectifier based on power electronics are required to convert the WT’s total rated output power to a level compatible with the utility power grid. The two more contemporary designs (both of which feature converters) enable the wind turbine to function in a variable speed mode, which can enhance the total amount of wind power collected by the turbine.
There are several ways to convert wind power into electricity, but the induction generator is the most popular choice. Wind power generation using a squirrel cage induction generator (SCIG)- is one of three primary wind farm (WF) designs now in use; a wind energy system using both a DFIG and a directly driven synchronous generator (DDSG) is explained in Figure 4.
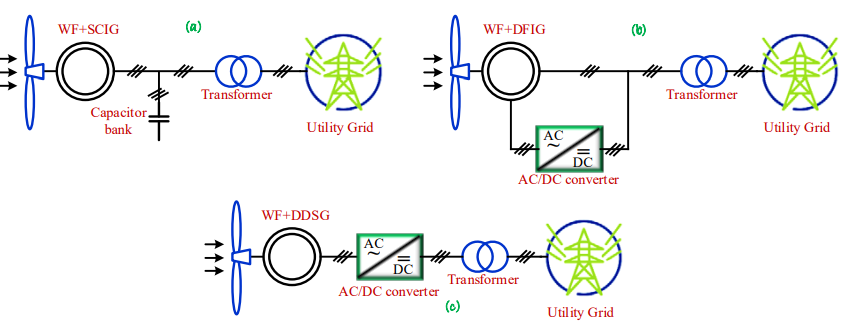
Figure 4 (a-c)
Figure 4a shows the WFs with SCIG, which is the most cost-effective approach because it is linked directly to the electrical network. It is common for a capacitor bank to be put at one of the wind turbine’s terminals to recompense the local reactive power created by the wind turbine, which fluctuates depending on how much power is generated. Back-to-back converters that only have a portion of their power supply are used to separate the frequencies of the mechanical and electrical rotors, as seen in Figure 4b. Last but not least, the WF with DDSG is shown in Figure 4c, where full power back-to-back (b2b) converters are utilized to disconnect the generator from the utility grid completely. In new WFs, it is becoming increasingly popular to have DFIG or DDSG linked to the grid through a b2b converter. However, half or more of the currently deployed WFs continue to use the SCIG architecture.
There have been many advancements in wind turbine technology since the early 1980s, but the basic concept has remained the same. To control the linked shaft speed, a horizontal rotor with three pitchable blades is used in the modern horizontal-axis wind turbine (HAWT) to harvest wind energy. This type of rotor has three blades and is widely used. It usually has a front bearing that is independent and is connected to a gearbox at a low speed, making it appropriate for the most common types of four- and two-pole generators. On the vertical-axis wind turbine (VAWT), the shaft’s axis is vertical and perpendicular to the ground, allowing it to rotate freely. When the wind is blowing, VAWTs always face the wind.
In general, the modern wind industry faces a major problem in designing the most efficient wind turbines to harness wind energy and produce electricity. It has taken the wind turbine industry 30 years to go from an idealistic fringe activity to a major player in the power production industry since the turbines have grown in size by a factor of 100 and engineering foundation and computational tools have evolved to accommodate the machine’s scale and volume. This has been a great wind turbine narrative up to this point; nevertheless, there are still many technological obstacles to overcome and many more spectacular feats to come.
Consequently, this approach necessitates careful control, modeling, and choosing a suitable wind power system. The widespread use of wind power has been directly tied to the development of the technology for wind turbines and control technologies over the previous two decades. In this regard, about 102 GW of wind power capacity was added in 2021. Annual increases raised the total capacity by 13.5%, reaching more than 845 GW. In terms of market share, China dominated the market, followed by the USA, UK, Brazil, and Vietnam. Figure 1 indicates growth in installed global wind capacity to approximately 845 by the end of 2021 compared to 651 GW in 2019. It is expected that installed wind capacity will increase dramatically over the next few years due to the continuing desire for alternative energy sources.
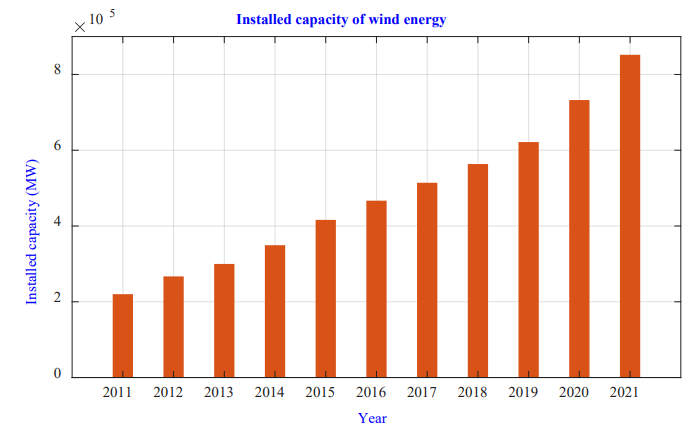
Figure 1
Despite the incredible expansion of wind energy, researchers face numerous hurdles, including the unpredictability of the wind’s nature, grid connection, and the positioning of wind turbines. This blog proposes a widespread review of the impact of converters on wind energy conversion with its operation, control, and related issues.
Wind Energy Conversion System
The wind energy conversion system (WECS) contains wind turbines and converters. Using wind turbines to extract the wind’s mechanical energy, the generators convert it into electrical energy, and the converter system is in charge of transferring the generated energy to the power network or a battery bank. When converting wind energy to electricity at a variable speed, the most commonly utilized generators are synchronous and doubly-fed induction generators (DFIG). When using induction generators, the rotor and stator are both linked directly to the network, but the electronic converter acts as a mediator between the two. Since the rotor circuit may independently change the amplitude and frequency of the produced voltage, the DFIG has long been the preferred choice for large, variable-speed WECS that are connected directly to the electrical network, as illustrated in Figure 2a.
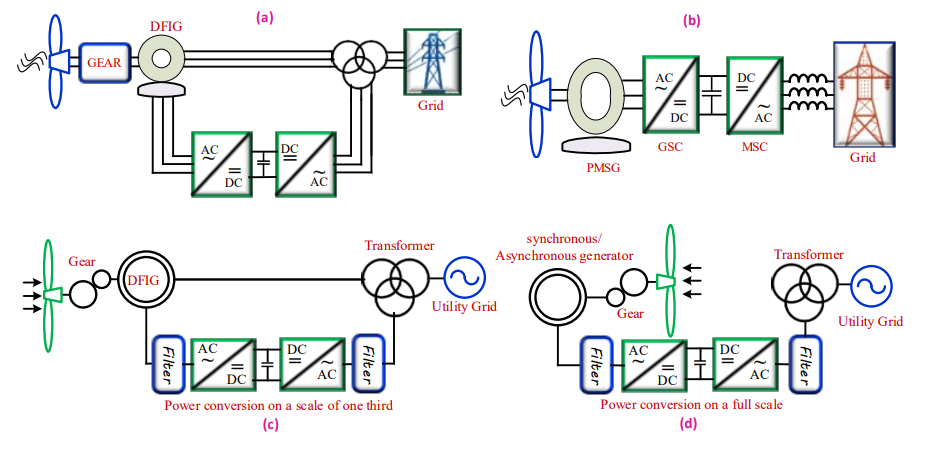
Figure 2 (a-d)
Generators that generate synchronous power are disconnected from the power distribution grid. As a result, they are included in systems that utilize full-scale converters. Due to the lack of a gearbox, the multipole permanent magnet synchronous generator (PMSG) has been the preferred alternative in recent years, reducing WECS losses, reducing maintenance requests, and enhancing system efficiency and dependability.
Figure 2b illustrates its configuration. Dc-links frequently employ a chopper circuit to disperse power in the event of grid disruptions. When compared to DFIG, PMSG offers the following advantages: no external stimulating current is required; high reliability; lightweight; low maintenance; small size; and high efficiency. The fundamental elements of a WTS’s control system, including the turbine, generator, filter, and converter, as displayed in Figure 2a–d. It is possible for the designed wind turbine to either be of the kind seen in Figure 2c or of the kind depicted in Figure 2d.
Previously, the usage of permanent magnet synchronous generators was recognized primarily in tiny WT but not in large-scale power generation due to the huge and heavy permanent magnets required. The usage of wind turbines based on permanent magnet generators (PMG) is quickly increasing because of the advancement of semiconductor switches and the improvement in efficiency and reliability; also, the innovation of materials utilized in the rotor of the generator has permitted the use of PMG at high power. For example, a permanent magnet-based-high-temperature superconductor is used in the rotor to achieve higher magnetic density: a 15-mm thick segment of permanent magnets can generate the same magnetic field as a 100–150-mm section of copper windings. Furthermore, the setting up of a gearbox, which is mandatory for large and medium WT, can be avoided using direct drive variable speed. Due to its simplicity, the direct drive wind turbine with PMG is now employed in the wind power system as the most promising one.
Wind Turbine Operation
The WECS uses improved control algorithms due to the rapid advancement of industry expertise. In a WECS, the wind’s kinetic energy is transformed to mechanical one using the WT, which is subsequently transformed into electrical energy. Because wind power is not ready to be integrated into the grid, several converter topologies have been developed to properly govern the grid-side converter (GSC) and the machine-side converter.
As a response, the fundamental control of WECS is used to serve the electricity network’s needs at different wind speeds, as presented in Figure 3a. The unpredictable nature of the speed of the wind and the variability of the climate highly influences wind energy’s dependability. Because of this, it is essential to understand the nature of wind and identify its operating areas to effectively integrate the WTs into the utility grid according to the speed measured. Thus, for a particular range of the speed of wind constrained by cut-out (Vcut-in) and cut-in (Vcut-out) speeds, WT can be used to harvest the accessible wind power, as explained in Figure 3a,b. The typical variable and fixed wind speed power curves are shown in Figure 3b.
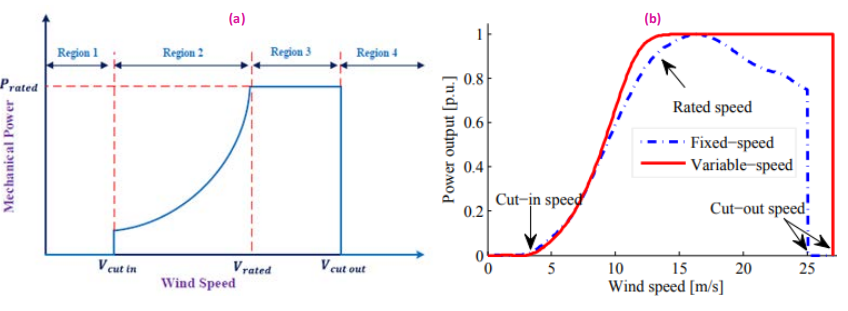
Figure 3 (a-b)
- Regions 1 and 4: As a result of safety concerns, it is necessary to stop and disconnect the WT from the electrical power network.
- Region 2: Wind power is harvested to its fullest potential in the central region using MPPT systems.
- Region 3: WT blades are protected from mechanical stress at high wind speed by limiting the generated power to its rated output through pitch angle control.
Wind Turbine Configurations
In a WT, the kinetic or mechanical energy of the wind is converted into electricity. When connecting WTs to electrical grids, three primary configurations may be utilized for this purpose. An induction machine is a typical cage-rotor induction generator that is promptly linked to the utility grid without needing a power exchanger. Reactive power is necessary for the induction machine to work. Both the utility power system and machine terminal capacitors can be used for this purpose. These devices are incapable of delivering any reactive power. DFIGs are used in the second kind of design, which involves the usage of a wound-rotor. Slip rings are used to capture electricity from a rotating rotor at a slip frequency. This ac power must flow via a converter-based rectifier and inverter system to be converted to a voltage and frequency compatible with the electric power system. Because of this configuration, the size winding of the stator generator can be reduced by 25–30%, with the converters compensating for the power discrepancy between the generator and rotor power. On the other hand, the expense of converters increases the overall cost of such a system. Variable voltage and variable frequency outputs are produced using a permanent or conventional magnet synchronous generator in the third kind of WT architecture. Therefore, an inverter and rectifier based on power electronics are required to convert the WT’s total rated output power to a level compatible with the utility power grid. The two more contemporary designs (both of which feature converters) enable the wind turbine to function in a variable speed mode, which can enhance the total amount of wind power collected by the turbine.
There are several ways to convert wind power into electricity, but the induction generator is the most popular choice. Wind power generation using a squirrel cage induction generator (SCIG)- is one of three primary wind farm (WF) designs now in use; a wind energy system using both a DFIG and a directly driven synchronous generator (DDSG) is explained in Figure 4.
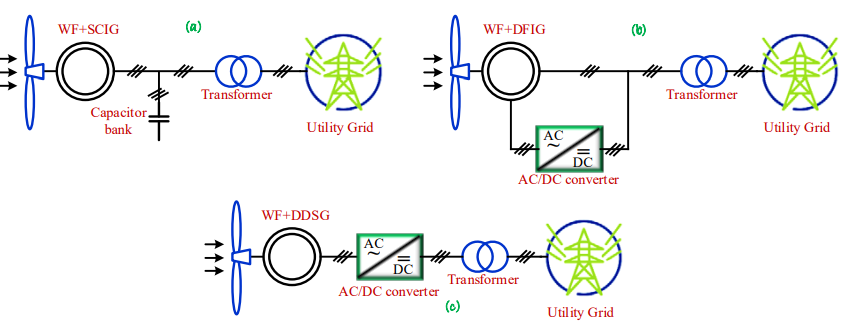
Figure 4 (a-c)
Figure 4a shows the WFs with SCIG, which is the most cost-effective approach because it is linked directly to the electrical network. It is common for a capacitor bank to be put at one of the wind turbine’s terminals to recompense the local reactive power created by the wind turbine, which fluctuates depending on how much power is generated. Back-to-back converters that only have a portion of their power supply are used to separate the frequencies of the mechanical and electrical rotors, as seen in Figure 4b. Last but not least, the WF with DDSG is shown in Figure 4c, where full power back-to-back (b2b) converters are utilized to disconnect the generator from the utility grid completely. In new WFs, it is becoming increasingly popular to have DFIG or DDSG linked to the grid through a b2b converter. However, half or more of the currently deployed WFs continue to use the SCIG architecture.
There have been many advancements in wind turbine technology since the early 1980s, but the basic concept has remained the same. To control the linked shaft speed, a horizontal rotor with three pitchable blades is used in the modern horizontal-axis wind turbine (HAWT) to harvest wind energy. This type of rotor has three blades and is widely used. It usually has a front bearing that is independent and is connected to a gearbox at a low speed, making it appropriate for the most common types of four- and two-pole generators. On the vertical-axis wind turbine (VAWT), the shaft’s axis is vertical and perpendicular to the ground, allowing it to rotate freely. When the wind is blowing, VAWTs always face the wind.
In general, the modern wind industry faces a major problem in designing the most efficient wind turbines to harness wind energy and produce electricity. It has taken the wind turbine industry 30 years to go from an idealistic fringe activity to a major player in the power production industry since the turbines have grown in size by a factor of 100 and engineering foundation and computational tools have evolved to accommodate the machine’s scale and volume. This has been a great wind turbine narrative up to this point; nevertheless, there are still many technological obstacles to overcome and many more spectacular feats to come.
Post a Comment:
You may also like:
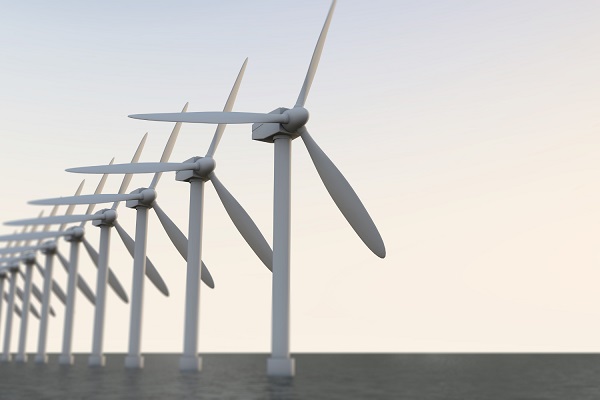
Featured Articles
Technical Potential for Wind Energy
The theoretical potential for wind, as estimated by the global annual flux, has been estimated at 6,000 EJ/yr. The global ...
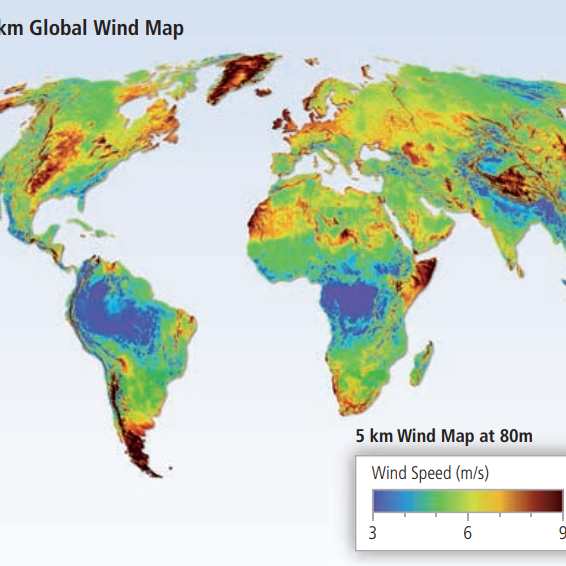
Wind Energy Background
The kinetic energy in the wind is a promising source of renewable energy with significant potential in many parts of the world. ...
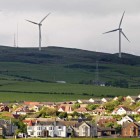
What Are the Advantages of Wind Energy?
Wind power is the fastest-growing source of electricity worldwide. The American Wind Energy Association estimates that more ...
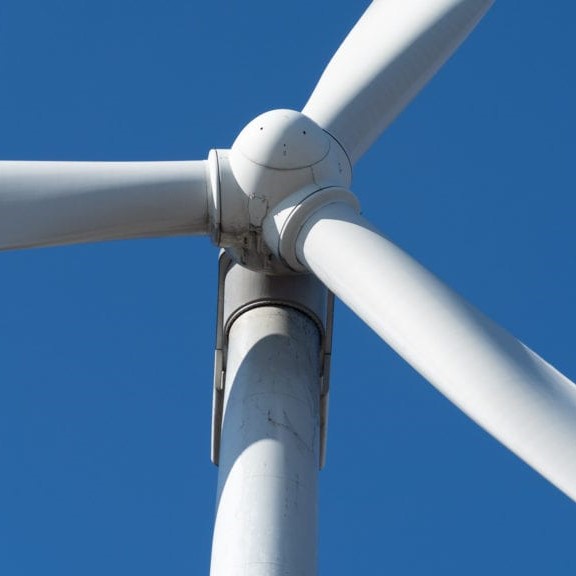
How Wind Energy is Collected and ...
Wind energy is a form of solar energy. Earth’s atmosphere is unevenly heated by solar radiation and the air is in constant motion ...
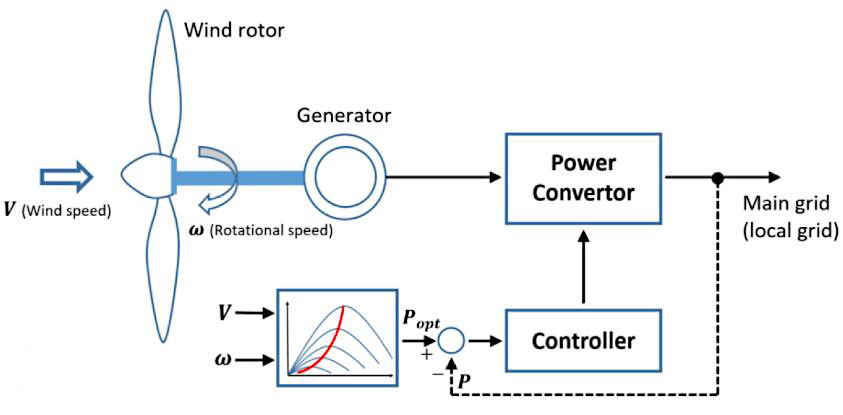
What is the Wind Energy Conversion ...
Due to technical and economic visibility, wind power has emerged as one of the most promising renewable energy sources ...
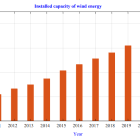